Purchase and price of the latest types of bitumino brand
As a base or binder course, bituminous penetration macadam or grouted macadam is utilized in road construction. In the following steps, the process of laying this material is explained in detail.
bituminous coal
Construction of the BermsIt is required to construct the berms before laying the pavement because the penetration kind of road does not typically have any curb at the borders of the roadway.
The specs should call for berms that are at least 5 feet wide, and each of these berms should be thoroughly rolled in order to stop the stone from shifting to the side as it is being rolled.
To roll these berms in the most efficient manner possible, start at the outer edge of each berm and work back and forth towards the center while the stone is being rolled.
This should be done as the stone is being rolled. It is recommended that the finalized grade of the road be brought up to the level of the top of the berm.
It is recommended that French drains be constructed on both sides of the road at each low point in the slope in order to channel the water through the berms.
On slopes that are longer than 400 feet, intermediate drains should be constructed. The distance between these drains should.
be determined by the nature of the previous roadbed as well as the drainage characteristics in the surrounding area. It is imperative that the roadbed have sufficient drainage.
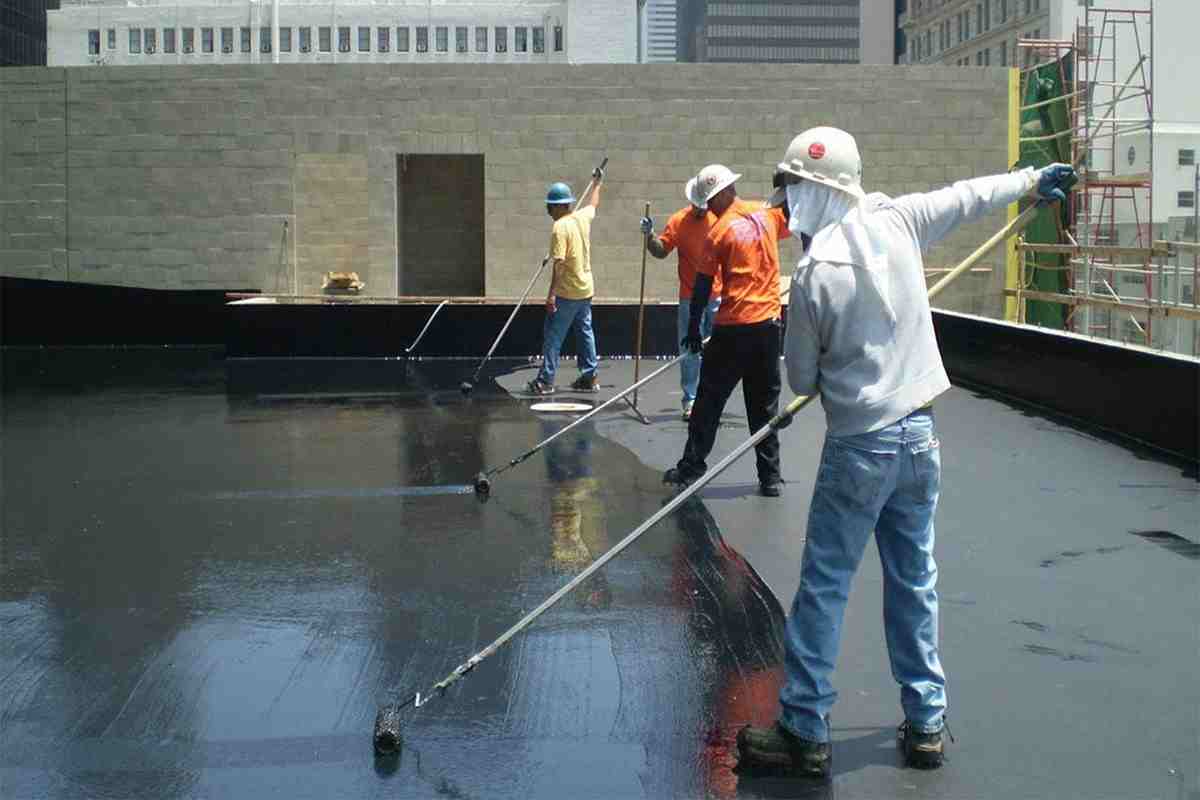
Salvaging Old RoadsIf the existing road is solid enough, it can be used as the foundation for the new road being constructed using the penetration method, which is one of the benefits of this type of road.
Almost all of our roads have been graveled or stoned numerous times and have metal surfaces of varying thicknesses. In regions with eight inches of densely packed metal.
we do not believe it is necessary to establish a foundation. In the majority of situations, the surface is uneven and lacks the proper crown; therefore, it is necessary to scarify the road and use a grader to smooth the surface and provide the proper crown.
If the metal is thinner than 8 inches in any position or is narrower than the proposed pavement, the specifications must call for the.
building projects of either a 4-inch water-bound course built on top of the metal over the old roadbed or the building up of the edges with two 4-inch water-bound courses so that the base is solid across the entire width of the road.
This will guarantee the road's integrity throughout its whole. The objective of the obstacle course is not to carry all of the weight, and the base must be stable and level for us to have a smooth riding surface.
The French drain that was previously discussed should be constructed at a suitable depth to permit complete drainage of the base course.
Frequently, these drains can be made using rejected stone or stone that failed the rolling process. Despite the relatively low cost, the added value to the road is rather substantial.
After the base has been made smooth and solid and elevated to the proper height, a layer of high-quality stone should be laid using a spreading mechanism attached to a truck or by hand if the stone is deposited outside the road's limits.
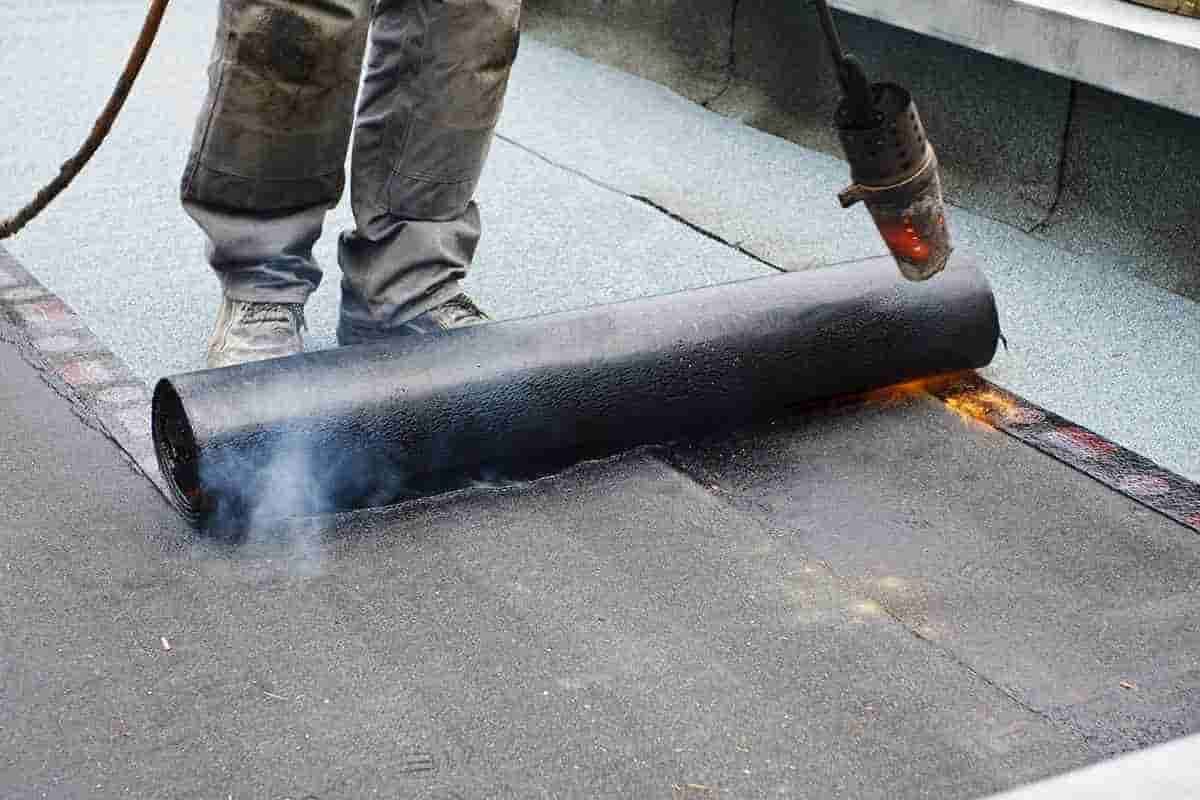
bituminous meaning in hindi
This can be accomplished with a truck and a spreader. This layer's maximum thickness is determined by the degree to which the base is solid.
It shall not be less than or greater than 3 1/2 inches, with both measurements referring to the thickness after rolling or the thickness after compacting.
If it is 3 inches or thicker, it should be made of No. 1 stone; otherwise, it should be made of No. 2 stone. On both sides of the road, forms must be placed prior to the application of the stone.
These forms must be aligned with the actual road's line and gradient so that when a crown board is passed over them, the resulting stone thickness will be uniform over the whole roadway.
The stone should next be rolled until it is firm using a self-propelled, three-wheeled roller weighing at least 10 tons. Any depressions that form in the.
stone during rolling should be filled with additional stone of the same grade and size as the original stone. After the bituminous material has been applied.
there is very little room for adjusting the road's surface, therefore it is essential that you keep this in mind as the road's completed surface is being fitted.
If the stone has been crushed by the roller to the degree where it fills the voids, or if its corners have been broken off to the point where it cannot be compacted, then that piece of the stone.
must be removed, and new stone must be laid, and the rolling process must proceed as normal. After the stone has been brought to a uniformly.
flat and tightly compacted surface, it should be cleaned of any leaves, sticks, or other debris that could impede penetration if not removed.
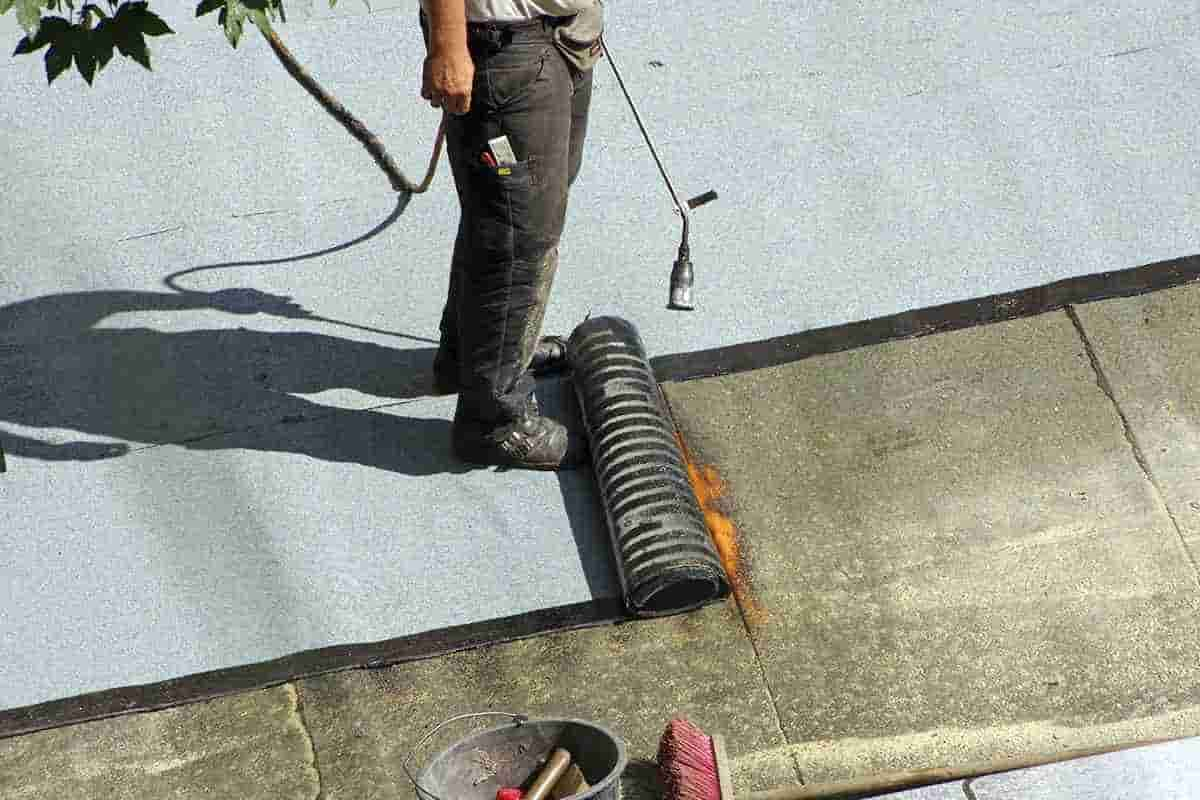
bituminous macadam road
Application of Bituminous Materials
After the surface has been painstakingly cleaned as detailed above, a power pressure distributor should be used to spread a bituminous binder, such as tar or asphalt, on the surface.
This procedure is required after the surface has been thoroughly cleaned. In the specifications, it must be stipulated that the material meets the standards for the grade to be laid, regardless of whether tar or asphalt will be used.
To ensure that each vehicle follows these requirements, it should be inspected in a testing center that has gained the appropriate accreditation.
If it is possible to arrange for the vehicle to be sampled at the point of loading, then the vehicle can be sealed, and testing can be conducted while the vehicle is en route, a substantial amount of time will be saved.
If the material passes the tests, it will be ready for use as soon as it is transported to the location where it will be utilized.
It is crucial to closely monitor both the air temperature and the temperature of the bituminous material. When the air temperature is below 40 degrees Fahrenheit, bituminous substances should not be applied.
Before applying tar, the temperature must be raised to around 250 degrees Fahrenheit. Before applying asphalt on a road.
it should be heated to around 350 degrees Fahrenheit. Approximately 1.5 gallons of bituminous material per square yard should be applied as the first layer.
After this has been applied, adequate amounts of keystone should be spread across the road to cover the voids, and then the road should be rolled over again.
It is suggested that this stone be gathered from stockpiles positioned along the road prior to the distribution of the surface course of stone.
Because an excessive amount of this keystone would be crushed on top of the larger stone and hamper the application of the second layer of bituminous.
material, it should be used solely to fill the voids. The temperature of the surroundings as well as the dimensions of the utilized keystone will have a significant impact on the rolling at this stage.
After the road has been rolled until it returns to its solid form, it should be swept to remove dust and excess stone, and then a second application.
of approximately half a gallon of bituminous material per square yard should be applied in the same manner as the first. The road should next be covered with a layer of No.
6 stone and rolled over again. It is recommended that adequate quantities of this stone be used to cover any surface spaces, but not enough to form a mat on the road.
After this has been completely compacted, the third and final layer of bituminous material should be put in the same way as the first and second layers. The recommended application rate is 1/3 gallon per square yard.
After this treatment has been applied, a thin layer of stone should be evenly placed across the road's surface before the road is opened to traffic.
For more information on different grades of bitumen suitable for your application, feel free to contact us.

How useful is this article to you?
Average Score
5
/
Number of votes:
1